- Solutions & Products>
- Color Harmony
Color Harmony
How to Achieve a Color Match in An Assembled Component
The issue of color harmony is a topic of great discussion amongst molders required to match various substrates in an assembled component. With proper color development and quality control procedures, the process of harmonization is not difficult.
To successfully implement a color management program designed to create color harmony in an assembled component, at least the following elements of the assembly must be considered:
- Color formulation
- Substrate
- Grain
- Gloss
- Part position
- Light source
- Color instrumentation
- Master/target
Color formulation
In order to assure that each part of an assembly is harmonized with its mating counterpart, it is important that the reflectance curve of the master/target is considered. The color formula for each part should contain identical pigments. This will assure that each part of an assembled component will be harmonized under one or more light source(s).
In order to make this possible the resin molded at the highest temperature will be the first formula considered. This will assure that each subsequent molded part will have a temperature stable color formula.
Substrate
Engineering requirements typically determine which polymers will be used for each part of an assembly. Not all polymers affect appearance the same. Molding temperature, fillers, gloss, melt flow and part configuration may affect color. As a result, it becomes important to assure that the molded part not only matches the master but is in the same quadrant of color space as its mating counterpart.
Grain
In an assembly, often there is more than one grain/texture to be considered when achieving color harmony. The grain of a part affects the reflection and scattering of light and, subsequently, its appearance. As it is with the substrate, it becomes important to assure that the molded part not only matches the master but is in the same quadrant of color space as its mating counterpart.
Gloss
The gloss of each part in an assembly is the single element, within the molders control, that can affect visual color harmony. It becomes critical that a gloss target and gloss specification is determined and that the specification is compliant to visual harmony. Once established, the molder has the responsibility to assure that molded parts meet the gloss specification. If the gloss of the molded parts is in compliance, visual harmony will be achieved and easily maintained.
Part position
During the development process, it is important that molded parts are evaluated visually in a controlled lighting environment and viewed in the part’s intended position in the assembly. The angle of view in any evaluated part can affect the appearance of the part as it pertains to gloss and color. To assure that the assessed results are applicable, the part must be viewed in part position. Any other position/angle is not applicable and, therefore, should not be considered. Once approval has been achieved, the part position is no longer relevant as production quality control will take over from here.
The most important element of viewing position, during production quality control, is that the part is viewed at the same angle of reflected light each and every time. This does not mean that the angle must be part position. It simply means that the viewing procedure must be consistent. Often, the best way to assure that this is in practice is by writing a color evaluation procedure that specifically identifies how a part will be viewed during production quality control.
Light source
During the development process, all applicable light sources must be considered. Typically for most industries, this would be day light, incandescent light and fluorescent light. The purpose of considering all light sources is to assure that the molded part is matching the master/target in the specified light(s). By doing so, the molder can assure that a metamerism (mismatch between one or more light sources) does not exist. If it is discovered that a metamerism does exist, it is the responsibility of the color supplier to correct the condition. This might require a reformulation of the color. Once approval has been achieved, the light sources are no longer relevant as production quality control will take over from here.
Once the part is in production, the primary light source is all that requires consideration by the quality department. If a part is determined to be non-metameric (i.e. matching in all specified light sources) during development, it will always be non-metameric in production. The reason this is true is because metamerism is the product of the color formula. Once approved, the formula shall never change.
Color instrumentation
Spectrophotometers are an important tool that should be used to assure color consistency and subsequently color harmony. While the device is capable of identifying color variation, it may not be capable of assuring that a specific color tolerance will yield an acceptable color match. This is because varying substrates (and gloss) reflect and scatter light differently. In order to achieve spectral results that best correlate with what we see visually, the target sample must be considered.
For high gloss (regular) surfaces, a 0/45 geometry is the preferred spectrophotometric technology. For textured (irregular) surfaces, a d8 (spherical) geometry is the preferred spectrophotometric technology.
Master/target
While it would seem obvious that the OEM master should be the target for controlling color in production, this is not always the case. If the color evaluation procedure is defined to be visual only (no instrumentation in use), the OEM master should be the preferred target. If the color evaluation procedure is defined to be visual and/or instrumental (spectrophotometric), the design approved PART should be defined as the target.
Here is how the procedure works:
Step 1: Select a part that represents a visually acceptable part. Establish this part as the standard part.
Step 2: Measure and store the standard part into a color computer under predetermined conditions.
Step 3: Store the physical standard in a clean and controlled environment. Always handle the standard with care (i.e. wearing protective gloves).
Step 4: Establish a filing system for each color that will be tested.
Step 5: Upon molding of a part colored with a new lot of colorant, view and compare the molded part in a controlled environment (light booth, under daylight conditions) to the standard part. Always handle the parts with gloves.
Step 6: Measure the molded part on the color computer to the stored standard part and save the lot data into history. Label and store the molded part into the history file.
Step 7: Conduct this procedure at a predefined frequency during the “run” of the parts to minimize the effect that variation might have on quality.
By using the design approved part as the target, we can eliminate the following variation from the color quality evaluation process:
- Substrate
- Gloss
- Grain
- Molding machine
- Tooling
- Color formula
By eliminating these variables, the only variation to be considered will be the lot number of the colorant. This becomes a pure evaluation of color and not an evaluation of variables.
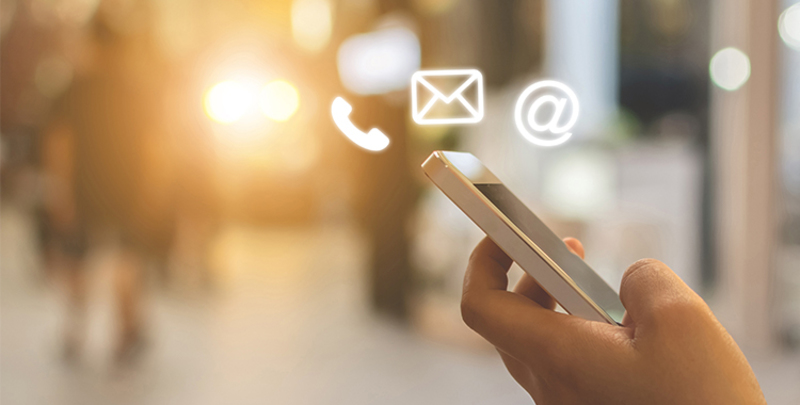
Contact Us
Ready to start your project or have questions? We'd love to hear from you.